Often times in our lives, we’ll find that something is designed or made with a specific purpose in mind and often times they don’t just stay in their intended form – they can be used for other purposes as well.
This blog discusses the idea of how Bottle closure get made, what they’re designed to do, and how they change throughout the manufacturing process.
What does a Bottle Cap look like?
The process of making a Bottle closure starts with the design. The designer will need to consider the shape, size, and color of the bottle cap.
Once the design is finalized, the manufacturer will need to produce it. The process of manufacturing a bottle cap can be divided into three parts: molding, stamping, and finishing.
Molding is when the plastic is heated and shaped into the desired form. Stamping is when the plastic is cooled and has a pattern imprinted on it. Finishing is when the bottle cap is given a protective finish.
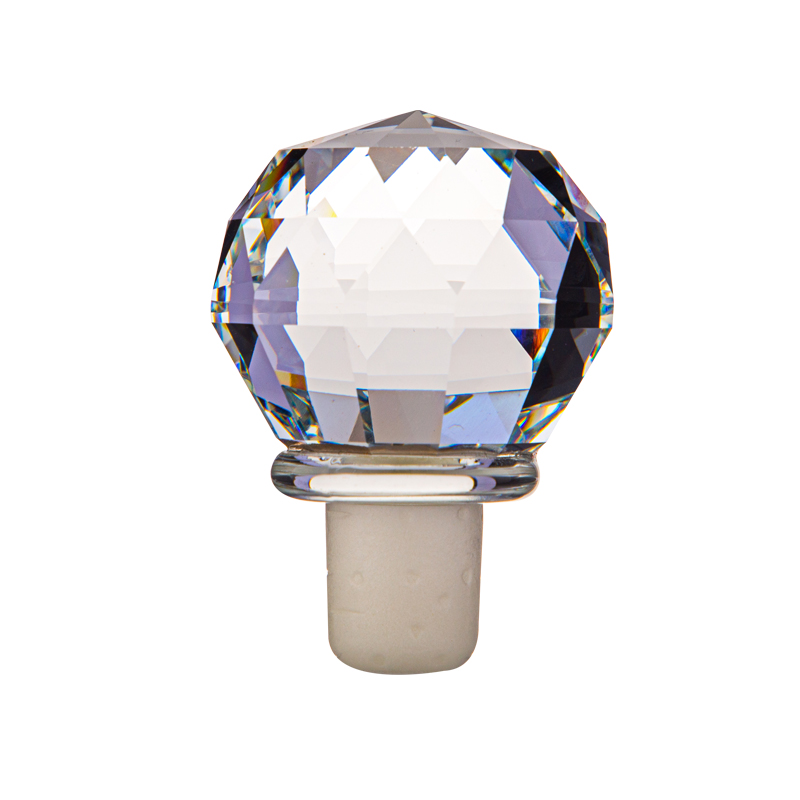
How are Bottle closure made?
The design and manufacture of bottle caps is a complex process that begins with designing the perfect shape.
Bottle closure are made from a variety of materials, including metal, plastic, and paper.
The first step in making bottle caps is to create a design for them.
This can be done using a variety of methods, including drawing on paper or using software. Once the design is approved, the manufacturing process begins.
To make the perfect bottle cap, the manufacturer must first understand the shape that they are trying to create.
The most common types of bottle caps are round, but there are also oval and triangular bottle caps.
The manufacturer must also consider the material that they will be using. Some materials, like metal, can be very difficult to work with and require special tools and techniques.
Once the design and material have been chosen, the manufacturing process begins. The manufacturer will typically start by casting the Bottle closure in metal or another suitable material.
After it has been cast, the manufacturer will then need to remove any excess material using a special technique known as milling.
After milling has been completed, the manufacturer will need to polish the cap to give it a smooth finish. This can be done using
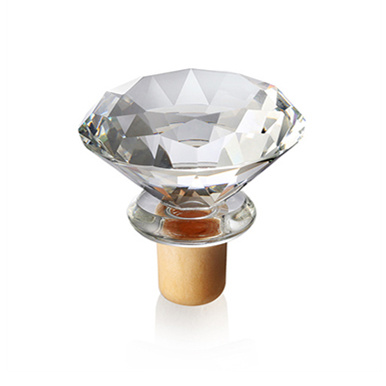
What is label design and printing like?
Label design and printing can be quite complex. It requires expertise in typography, layout, and graphics. Many companies outsource this task to specialized firms.
Bottle closure are often seen as badges of distinction, as they are made from a hard, durable plastic that can last for years.
They can also be customized to reflect the personality of the person wearing them. The manufacturing process for bottle caps starts with a design.
New packaging technologies
Designing and manufacturing bottle caps is a process that requires the use of some new packaging technologies.
Here are four ways these technologies are used to create bottle caps: injection molding, die casting, screen printing, and thermal transfer printing.
Injection molding is the most common way to create bottle caps. This process uses a heated metal die to create the cap from a plastic or other material.
Die casting is a similar process, but it uses a die instead of a heated metal die. Screen printing is a type of printing that uses a screen to print images on cloth or other materials.
Thermal transfer printing is a newer type of printing that uses heat to transfer ink from one surface to another.
The Future of Bottle Closures
The closure industry is constantly evolving, with new and innovative designs being created all the time.
Here, we take a look at the design process of some of the most popular bottle closures on the market today.
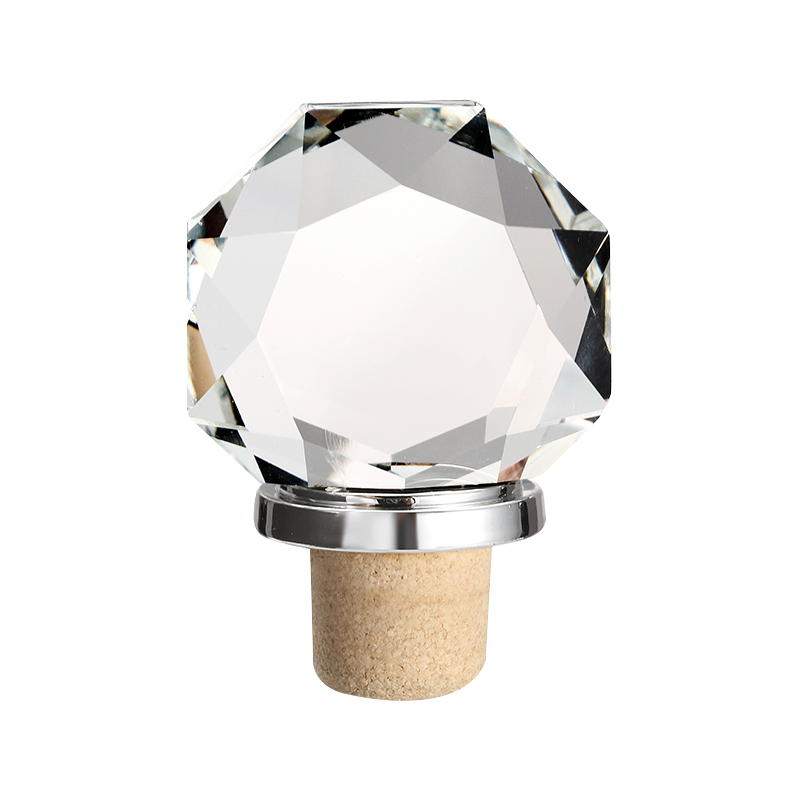
How Bottle closure Get Made – Designing And Manufacturing
Designing a bottle cap is a complex and time-consuming process, involving many stages and steps.
The first step is to come up with an idea for the cap, which often involves taking into account the product it will be used with and the branding requirements of the company producing it.
Once the design is finalized, it needs to be manufactured in a precise and accurate manner.
This can involve various stages of production, from designing and producing the actual caps themselves to ensuring they’re packaged correctly and shipped to retailers.
In short, designing and manufacturing a Bottle closure requires a great deal of expertise and skill, and fortunately, there are many companies out there that are capable of fulfilling this task.
How to Create a Design for a Bottle Closure
Designing and manufacturing bottle closures is a process that requires careful consideration of many factors.
The following tips will help you create a design that will be successful in the market.
- Study the current bottle closure designs on the market. Be aware of what features are popular and why. Pay close attention to how the designs are executed and what makes them appealing. This information can help you create a design that stands out from the competition.
- Think about what type of bottle closure design would be best for your product. Different types of products require different types of closures. For example, beverage bottles need a screw-on closure, while water bottles need a flip-top closure. It is important to choose a closure type that is suited for your product and will be popular among consumers.
- Consider the size and shape of your product when designing a bottle closure. Some closures are designed for certain types of bottles, while others are compatible with almost any type of bottle. It is important to pay attention to these details so your product looks its best on shelves.
- Choose a design that is easy to manufacture and produces high-quality results. Many factors must be
Conclusión
The process of designing and manufacturing bottle caps can be complex and challenging, but with the right tools and a bit of experience, you can get the job done efficiently and on time.
In this article, we will take a look at some of the key components that make up a bottle cap design, as well as discuss some common manufacturing challenges that designers and manufacturers face.
By understanding these concepts, you will have a better foundation from which to begin your own bottle cap design project.