Proveedor de tapas de botellas said that as an important part of the packaging industry, the aluminum-plastic cover plays a key role in the sealing of the product.
It not only plays a role in safety, but also has the function of anti-theft. So how to judge the quality of the aluminum plastic cover from the appearance?
Bottle closure supplier:Check the riveting points
Bottle closure supplier said that The size of the riveting point is the same, the surface should be smooth, the thickness is uniform, there is no burr around, and the color is the same as the color of the plastic cover itself.
Bottle closure supplier said that The diameter of the riveting point of the aluminum-plastic cover is 1-1.5 mm larger than the diameter of the riveting hole of the aluminum-plastic cover (the flanging unilateral length of the flanged aluminum-plastic cover is 1-1.5 mm), and the automatic forming machine of the aluminum-plastic cover can fully meet the the above requirements.
Bottle closure supplier said that However, manual riveting will appear uneven on the surface, the periphery is not round, there are wiredrawing, burrs, etc., especially when riveting with manual electric heating tools, the temperature cannot be controlled, resulting in uneven heating of the riveting material, changing color, and even appearing Spotted.
Check clearance
Check the gap between the plastic cover and the aluminum cover.
Bottle closure supplier said that The bottle cap riveted by mechanical equipment is pressed while heating, and the plastic cover and the aluminum cover are tightly attached with no gap.
However, manual riveting cannot add pressure, resulting in a large gap between the aluminum cover and the plastic cover, which can shake up and down.
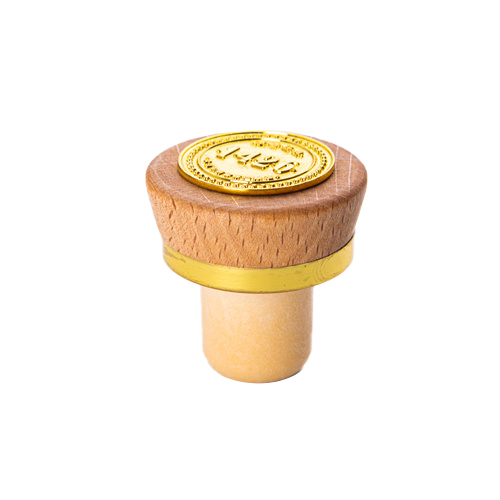
Check whether the aluminum cover is deformed
Bottle closure supplier said that Whether the edges of the aluminum-plastic cover are neat, whether the height of the aluminum cover meets the packaging requirements, and whether the aluminum cover has been oxidized (or coated), etc.
Bottle closure supplier said that The roundness of the aluminum cap directly affects the normal operation of the capping machine.
The matching gap between the inner diameter of the aluminum cap and the outer diameter of the bottle mouth should not be too large. Otherwise, wrinkles will appear when sealing.
4. Check the tear point of the aluminum cover
Check whether the tear point of the aluminum cover is flat after the aluminum-plastic cover is opened.
Bottle closure supplier said that Check whether the breakpoint burr is too large after the breakpoint aluminum-plastic cover is opened, and there should be no scratching feeling.
Check whether there are burrs or unbroken parts after the notched aluminum-plastic cover is opened. The notch should not be turned up and there is no scratching feeling.
5. Check the strength of the aluminum cover
In addition to the aluminum cover, the thickness of the aluminum material is also an important reason that directly affects the strength of the aluminum cover.
Bottle closure supplier said that The thickness of the aluminum cover material varies with the outer diameter.
Generally, for the aluminum cover with a diameter of 13–20mm, the thickness of the aluminum material is selected within the range of 0.18–0.2lmm; for the aluminum cover of 28–33mm, the thickness of the aluminum material is selected within the range of 0.23–0.25mm.
What are the factors that affect the processing of aluminum plastic cover?
The processing of aluminum-plastic cover often affects its processing progress due to some factors.
If it is not handled properly, it will directly affect the quality of aluminum-plastic cover molding, so these factors must be excluded before processing.
1.Process factors
(1) Bottle closure supplier said that The temperature of the material tube or the hot runner is too low, and the melt plasticization is incomplete. The temperature should be increased or the plasticizing time should be appropriately extended.
(2) The temperature of the mold is too low, resulting in a slowing of the flow rate of the melt, and the cooling is too fast, and the two streams cannot be effectively fused when they meet.
(3) The wall thickness of the aluminum-plastic cover product is too thin, and it is difficult to fill the mold, which increases the melt temperature difference in the aluminum-plastic cover mold, and the phenomenon of welding marks is easy to appear.
At this time, the injection pressure can be appropriately increased or the material barrel temperature.
(4) Bottle closure supplier said that The injection speed is too slow, resulting in a relatively slow material flow rate, and the melt in the first cavity is cooled faster.
2. Material factors
(1) The raw material has moisture, which is converted into gas during the injection process, which affects the fusion effect of the material flow.
The raw material should be dried and moisture-proof treatment should be performed on the raw material.
3. Mold factor
(1) Bottle closure supplier said that The gate design is unreasonable, and the gate position should be avoided as far as possible around the inserts and holes.
The gate where injection filling occurs should try to correct, migrate or add a stopper buffer, and try not to use or use as many gates as possible.
(2) The mold is trapped in gas, so that the gas in the cavity cannot be discharged. When the two streams are merged, the fusion effect is affected.