Bottle closure supplier said that Bottle caps are often seen in our lives, and the bottle caps used for different products are different.
What are the classifications of bottle caps by bottle closure supplier?
According to the function,there are ordinary rotating caps, anti-counterfeiting caps, anti-theft caps and nozzles.
Among them, sprinklers are mainly used in pharmaceutical packaging and cosmetic packaging, while anti-counterfeiting bottle caps and anti-theft bottle caps are mainly used in the wine packaging market.
Bottle closure supplier said that According to the material,there are cork stopper, butyl rubber stopper, alumina, tinplate, plastic, glass and so on.
Among them, cork stoppers are mainly used in wine packaging, and butyl rubber stoppers are mainly used in the pharmaceutical packaging market.
Bottle closure supplier said that According to the use,there are mainly wine bottle caps, which are mainly used in the packaging of wine bottles.
The materials are mostly aluminum and tinplate, and some use PP hard plastic.
Bottle closure supplier said that Beverage bottle caps are mainly used in the packaging of beverage bottles, mineral water bottles and medicinal bottles.
The main materials are PP and PE. Food bottle caps are mainly tinplate caps (used on canned glass bottles) and plastic caps.
Perfume bottle caps are mostly glass, plastic and alumina bottle caps.
Bottle closure supplier said that Ordinary health care product bottle caps are mainly rotary plastic bottle caps. This kind of bottle cap is very convenient for some patients or the elderly to use.
Bottle closure supplier said that Although it is not so unique on the shelf, it is highly accepted by consumers. The tear-off cap is relatively more convenient to use.
For some women with less strength, the health care product bottle packaged with the tear-off cap will make it very convenient for them to use.
In order to prevent children from misunderstanding, the anti-theft cap is also used in the packaging of health care products, which effectively prevents some accidents from happening, but at the same time, it is not convenient for ordinary consumers to open the anti-theft cap, and the cost is relatively high.
In order to improve the external quality of the products, the health care product bottle manufacturers have also applied a large number of anodized aluminum caps on the packaging of health care products bottles.
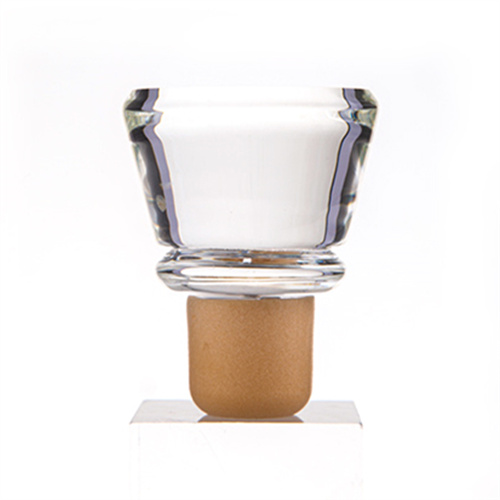
What is the spraying process of wine bottle caps?
Nowadays, there are many types of wine bottle caps on the market, and the shapes of all kinds of wine bottle caps are different, but their spraying process is roughly the same. Cover in detail.
1. Annealing
Bottle closure supplier said that Plastic is easy to form internal stress during molding, and it is easy to crack at the stress concentration after painting.
Annealing treatment or full surface treatment can be used to relieve stress.
Bottle closure supplier said that The annealing treatment is to heat the ABS plastic molded parts to below the heat distortion temperature, that is, 60 ° C, and keep it for 2 hours.
Bottle closure supplier said that Since this process requires a lot of equipment investment, the wine bottle cap can be treated with the whole surface technology, that is, the surface of the plastic part can be treated with a solution that can eliminate the internal stress of the plastic part at room temperature for 15 to 20 minutes.
2. Degreasing
Bottle closure supplier said that The surface of plastic parts is often stained with oil stains, hand sweat and release agent, which will make the paint adhesion worse, and the coating will crack, blister and fall off.
The spray line should be degreasing before painting.
The plastic parts are usually cleaned with gasoline or alcohol, and then chemical degreasing should be performed.
3. Electrostatic removal and dust removal
Bottle closure supplier said that Plastic products are insulators, and the surface resistance is generally around 1013Ω, which is easy to generate static electricity.
After being charged, it is easy to absorb fine dust in the air and adhere to the surface.
Bottle closure supplier said that Due to the difficulty of removing the electrostatically adsorbed dust by the general air blowing method, the use of high-voltage ionized air flow at the same time has a better effect of removing electrostatic dust.
4. Spraying
Bottle closure supplier said that The thickness of the plastic coating is 15~20μm, and it usually takes 2~3 sprays to complete.
After one spraying, let it dry for 15 minutes, and then carry out the second spraying.
Bottle closure supplier said that Surfaces that require a glossy finish must also be sprayed with a clear coat. The coated parts have little effect on the flame retardant properties.
5. Drying
After coating, it can be self-drying at room temperature or baked at 60℃ for 30min.