customized beverage packaging Market Demand Increases
In recent years, China’s customized beverage packaging industry has achieved rapid development. In the packaging of beverages, PET bottles have taken an absolute dominant position.
As market demand expands from time to time, the number of caps that respond to it has expanded.
In order to prevent fake and inferior products from flooding the market, including the quality of the contents from being maliciously destroyed, the current bottle caps are equipped with anti-theft structures.
customized beverage packaging technology upgrade
The packaging cost accounts for a large proportion of the beverage product cost, so how to improve the quality of customized beverage packaging and reduce the cost has attracted more and more attention from everyone.
The output and quality of plastic anti-theft bottle caps for beverage bottles mainly depend on production equipment and molds.
Therefore, the major domestic suppliers of customized beverage packaging materials have increased their investment in cap-making equipment, which has greatly improved the quality of bottle caps in the domestic market, reaching the world’s advanced level.
Therefore, in the field of plastic bottle cap production, the battle between injection molding and compression molding has also opened up.
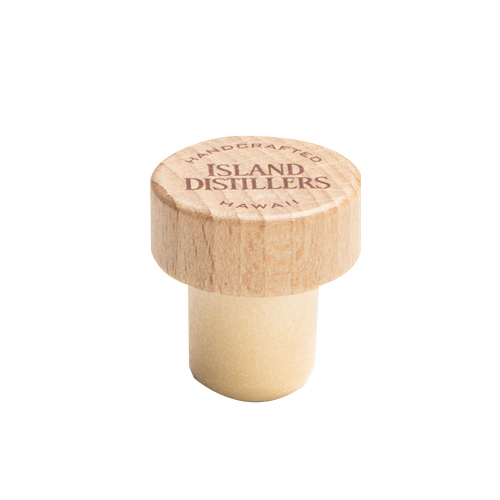
Upskilling is the driving force behind the development of customized beverage packaging
1) Structure and classification of plastic anti-theft caps for customized beverage packaging.
Although the bottle cap is not large in size, its structure is relatively complex, including sealing inner plug, thread, capping tooth line, connecting bridge and anti-theft ring, heat resistance, opening torque and breaking cover function, etc., to produce qualified cover products, there are high requirements on the precision of the mold.
There is a ring of sealing ring and inner thread in the lid, and the lower anti-theft ring has a ring of bosses on the inner and outer sides, and a thin bridge with a diameter of about 2 mm to 8 mm is connected to the bottle cap.
Once the bottle cap is opened, the bridge will break.
Typical injection mold structure for plastic anti-theft caps Plastic anti-theft caps for customized beverage packaging were first produced by injection molding.
After years of development, it has now formed a special injection molding machine for bottle caps and a supporting delivery and testing unit.
Most of the molds adopt the hot runner system and one mold with multiple cavities. 32 cavities, 48 cavities, 64 cavities, and 72 cavities are the current mainstream foreign mold cavities.
Caps belong to thin-wall injection molding, although the volume is small, but the structure is relatively complex.
There are structures such as thread and anti-theft ring, and the connection bridge between the customized beverage packaging and the anti-theft ring is relatively thin, making demolding become the most important difficulty in the injection mold of the bottle cap.
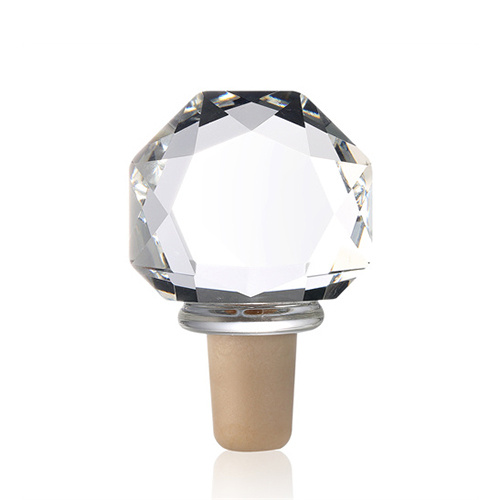
At present, there are mainly 3 mold methods to deal with the demoulding problem
One is that the anti-theft ring part adopts the Huff block method.
In the mold opening stage, the Huff block in the part of the anti-theft ring is first opened, and then the thread part is forced out, and finally the entire cover is ejected by the inner top cover.
The structure of this kind of mold is relatively simple, and usually only requires secondary demoulding, but the lateral volume of the mold is large, and the number of cavities is inevitably limited.
The second method is to directly force the thread without processing the connection bridge during injection molding, and add a ring cutting process after injection molding.
The customized beverage packaging cost of this kind of mold is relatively high, and a ring cutting machine needs to be added, which increases the production cost.
However, the mold structure is simple, the mold processing cost is low, and the mold life is long.
The third is to use a three-time demolding mechanism and one-time forming.
This kind of mold structure is relatively complex, and there is more relative movement between the mold parts during the injection molding process, so the manufacturing accuracy of the mold and the strength of the mold material, wear resistance, etc.
All have higher requirements, such as the common precision between the relatively moving parts is above H7 /.
When the plastic is injected into the cavity and fully cooled, first the cavity fixing plate is separated from the anti-theft ring fixing plate, that is, the movable and fixed molds are separated.
Secondly, the anti-theft ring is together with the central threaded core, middle core and ejector core.
The ejector moves forward, separates from the bushing, and separates the plastic product from the bushing to complete the first demoulding.
Then, the threaded core and the middle core stop moving, and the anti-theft ring core and the ejector core move forward together , that is, the center middle ejector is ejected, the outer anti-theft ring core is pushed out, and the inner thread and the inner convex ring of the anti-theft ring are forced out to complete the second demoulding.
Finally, the core of the anti-theft ring stopped moving, and the ejector core continued to improve, completely ejecting the finished plastic product from the core of the anti-theft ring, and completed the third demoulding.
So far the whole demoulding process is completed.
The reset of each core of the clamping mold is reset by the return rod, each connecting rod and the movable and stator cores, and one task cycle is completed.