Glass bottle closure is a type of plastic closure that can be used in glass bottles. There are many types of closures, but the most popular are twist caps, screw caps, and crowns. In this article we will explore the manufacturing process of these three types of closures.
Introduction
Glass bottle closures are hermetically sealed to preserve the freshness of contents and to prevent leakage. The manufacturing process for glass bottle closures begins with the batching of raw materials. These raw materials are melted in a furnace and formed into small pellets called cullets.
The cullets are then fed into a machine that forms them into the desired shape of the closure. After the closures are formed, they undergo a series of quality control tests to ensure they meet the required standards. Once they pass these tests, the closures are then packaged and shipped to the customer.
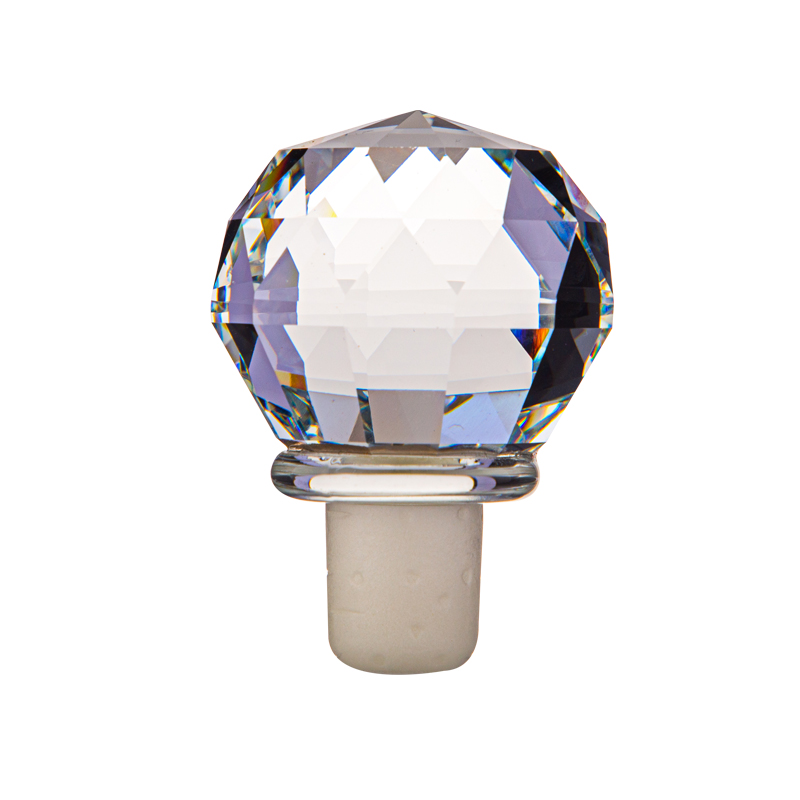
How Glass Bottle Closures are Manufactured
There are three main types of glass bottle closures: screw caps, roll-on pilfer proof caps (ROPP), and cork-and-plug. Screw caps are the most common type of closure, followed by ROPP. Cork-and-plug closures are typically only used for high-end wine bottles. The manufacturing process for each type of closure is slightly different.
Screw caps are made from a moldable plastic or metal. The top of the cap is molded into the desired shape and then cooled. A thread is cut into the inside of the cap, which will mate with the thread on the neck of the bottle. The bottom of the cap is then pressed onto a liner, which can be made from various materials such as foil, paper, or plastic.
ROPP caps are also made from a moldable plastic or metal. The top and bottom of the cap are molded separately. The two halves are then joined together and a thread is cut into the inside of the cap. A liner is then glued or welded onto the bottom half of the cap.
Cork-and-plug closures are made from natural cork that is compression molded into plugs that fit snugly into the neck of a bottle. A wire cage holds the cork in place and provides an easy way to remove the plug when opening the bottle.
The Process of Manufacturing Glass Bottle Closure
The process of manufacturing glass bottle closures is a multi-step process that begins with the raw materials being mixed together in a furnace. Once the desired compounds have been melted together, they are poured into molds where they will cool and solidify.
After the closure has cooled and hardened, it is then removed from the mold and undergoes a series of finishing processes. These may include being annealed (heated to relieve stress), grinding or polishing the surface, and adding any desired decoration. Finally, the closure is Inspected for quality before being shipped to the customer.
The Raw Materials of Glass Bottle Closure
To make a glass bottle closure, you will need the following raw materials:
-A piece of glass that has been cut to the desired shape and size
-A bottle cap that fits snugly on the neck of the bottle
-A piece of metal or plastic that will be used to seal the cap to the bottle
-A piece of rubber or cork that will be used to create a tight seal between the cap and the bottle
To begin, you will need to cut a piece of glass to the desired shape and size. Next, you will need to find a bottle cap that fits snugly on the neck of the chosen bottle. Once you have found a suitable cap, you will need to seal it to the bottle using a piece of metal or plastic. Finally, you will need to create a tight seal between the cap and the bottle using a piece of rubber or cork.
The Steps in the Production Process
After the glass bottle and cap are made, they must go through a production process in order to be transformed into a functional product. The steps in the production process are as follows:
- The first step is to assemble the bottle and cap. This involves putting the two pieces together and ensuring that they fit correctly.
- The next step is to apply a sealant around the edge of the cap. This ensures that the contents of the bottle will be sealed inside and will not leak out.
- Once the sealant has been applied, the final step is to test the product to ensure that it is leak-proof. If there are any leaks, they must be fixed before the product can be sent out for use.
Conclusion
We hope you have enjoyed learning about the manufacturing process of glass bottle closures. This type of closure is an important part of the packaging industry, and there are many different ways to produce them. With the right knowledge and equipment, any company can become a glass bottle closure manufacturer. If you are interested in starting your own business or becoming a supplier for this type of product, we encourage you to research the market and learn as much as you can about the manufacturing process.